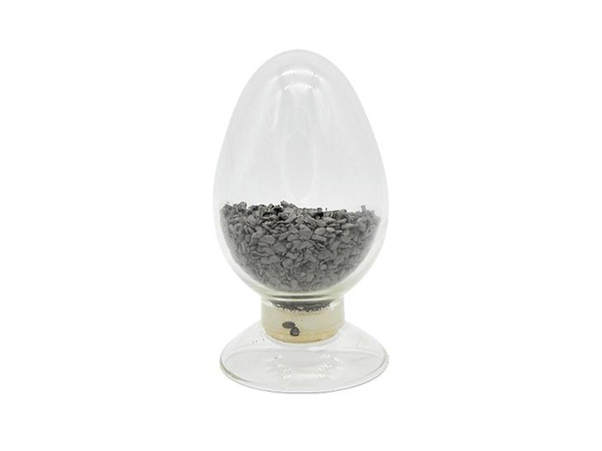
Optimizing Metal Injection Molding (MIM) Processes: A Comprehensive Defect Analysis
1. Introduction to Metal Injection Molding (MIM):
Metal Injection Molding (MIM) combines the flexibility of plastic injection moulding with the strength and integrity of wrought metals to achieve complex shapes and high-performance parts. However, like any advanced manufacturing process, MIM is not without its challenges. This article delves into the common defects encountered in MIM and provides a detailed analysis of their causes, with strategies for prevention and control.
2. The MIM Process and Its Industrial Significance:
MIM is particularly suited for producing small, intricate parts on a large scale, offering cost-effectiveness and efficiency where traditional manufacturing falls short. The process involves several critical stages:
a. Feedstock Preparation:
- Powder Selection: Choosing the right metal powder is crucial, as impurities can lead to defects during sintering.
- Binder Systems: The binder must be carefully selected and mixed to ensure it performs adequately during molding and is removed effectively during debinding.
b. Molding:
- Injection Parameters: Precise control of temperature, pressure, and injection speed is essential to produce defect-free parts.
c. Debinding and Sintering:
- Debinding Techniques: The debinding process must be carefully controlled to avoid defects such as cracks or warpages.
- Sintering: Uniform heating and a controlled atmosphere are key to achieving the desired part density and properties.
3. Analyzing Common MIM Defects:
Despite the advanced nature of MIM, defects can arise at various stages of the process. Understanding these defects is the first step towards mitigating them.
a. Short Shots:
- Cause and Prevention: Short shots occur when the mould is not filled completely. Optimizing material flowability, mould temperature, and injection parameters can address this issue.
b. Weld Lines:
- Cause and Prevention: Weld lines are formed when separate flows of molten material meet but do not unite properly. Increasing injection pressure and temperature can help reduce this defect.
c. Porosity:
- Cause and Prevention: Porosity can be caused by trapped air or gases during moulding. Proper venting and gas elimination strategies are critical to prevent this defect.
d. Distortion:
- Cause and Prevention: Distortion can occur due to uneven cooling or internal stresses. Uniform cooling and careful design of the part and mould can mitigate this defect.
4. Advanced Strategies for Defect Prevention in MIM:
Preventing defects in the intricate MIM process requires a multifaceted approach that integrates cutting-edge technology, meticulous planning, and continuous improvement. Here are some advanced strategies that Moat City employs to minimize defects and ensure the production of high-quality MIM components:
a. Material Characterization and Optimization:
- Feedstock Homogeneity: Ensuring the homogeneity of feedstock is critical. This involves rigorous testing of powder particle size distribution, shape, and purity, as well as the binder components’ viscosity and thermal behaviour.
- Custom Binder Formulation: Developing custom binder systems tailored to specific powders can improve the debinding process, reducing the risk of defects such as cracks or warpage.
b. Precision Molding Process Control:
- Real-time Monitoring: Implementing sensors and control systems for real-time monitoring of injection parameters allows for immediate adjustments, ensuring consistent quality throughout the production run.
- Process Simulation: Using advanced simulation software to predict and analyze the flow, cooling, and solidification of the metal within the mould can identify potential issues before production begins.
c. Debinding and Sintering Excellence:
- Controlled Debinding: Applying a carefully controlled, multi-stage debinding process that accommodates the thermal and chemical removal of the binder can prevent defects associated with uneven binder removal.
- Optimized Sintering Profiles: Developing specific sintering profiles for different materials and geometries ensures uniform densification and minimizes distortion or shrinkage.
d. Design for Manufacturability (DfM):
- Component Design Review: Collaborating closely with clients to review component designs for manufacturability, suggesting modifications that can reduce stress concentrations and improve mould filling.
- Mould Design Optimization: Utilizing state-of-the-art CAD and CAE tools to design moulds that facilitate optimal temperature control and material flow, thereby reducing the likelihood of defects.
e. Quality Assurance Protocols:
- Comprehensive Inspection: Employing a combination of visual inspection, dimensional measurement, and advanced techniques such as X-ray imaging and computed tomography (CT) to detect internal defects.
- Statistical Process Control (SPC): Using SPC methods to monitor and control the manufacturing process, identifying trends that could lead to defects and implementing corrective actions proactively.
f. Continuous Improvement and Training:
- Employee Training: Regular training programs for employees to stay updated on the latest MIM technologies and best practices in defect prevention.
- Feedback Loop: Establishing a robust feedback loop that incorporates insights from production, inspection, and field performance to continuously refine processes and designs.
By integrating these advanced strategies into every phase of the MIM process, Moat City ensures that each component meets the highest standards of quality and performance. Our commitment to excellence in MIM production is unwavering, as we continuously seek to innovate and improve upon our processes.
5. Conclusion:
Metal Injection Molding (MIM) is a sophisticated process that demands a deep understanding of materials science, engineering, and process control. By analyzing and addressing common defects, Moat City is at the forefront of enhancing the quality and reliability of MIM components, driving innovation in the industry.
6. Contact Details:
For further information on optimizing your MIM processes and reducing defects, reach out to Moat City’s experts.
Email: rongqi.chen@moatcity.com
Web: www.moatcity.com
WhatsApp: +447983626714
Our team is ready to support your MIM needs and help you achieve the highest standards in your products.
Leave a Reply