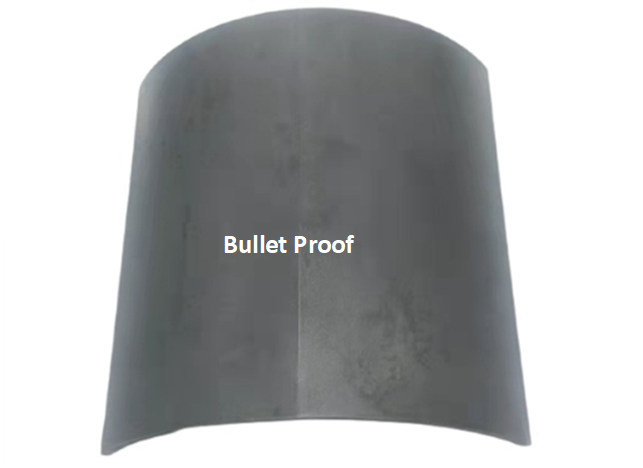
Bulletproof Ceramics: Boron CarbideHot-Pressing vs Pressureless Sintering
1. Introduction to Bulletproof Ceramics:
Bulletproof ceramics have carved a niche for themselves in modern armor systems. Their high stiffness-to-weight ratio, high strength, and chemical inertness make them indispensable. Among the materials used for bulletproof ceramics, boron carbide (B4C) is particularly noteworthy. This article aims to provide an in-depth understanding of boron carbide and compares two primary sintering methods: hot-pressing and pressureless sintering.
2. The Marvel of Boron Carbide:
Boron carbide is a superhard material, second only to diamond and cubic boron nitride in terms of hardness. It has a range of impressive properties that make it a prime candidate for various high-end applications.
a. Unique Properties:
- High Melting Point: Boron carbide has a melting point that exceeds 2200°C, making it suitable for high-temperature applications.
- Low Specific Gravity: Its low density makes it ideal for lightweight armour systems, contributing to its widespread use in military applications.
- Chemical Inertness: Boron carbide is chemically inert in many environments, which enhances its longevity and makes it a reliable material for long-term applications.
3. The Sintering Dilemma:
Sintering boron carbide is a challenging task. The covalent bonding structure of boron carbide requires temperatures above 2200°C for effective sintering. This section will delve into the pros and cons of the two most commonly used sintering methods.
a. Hot-Pressing:
- High Density: Hot-pressing can achieve relative densities of up to 91.6%, making it a preferred method for applications that require high-performance materials.
- Cost: This method is expensive due to the high temperatures and pressures involved. It is usually reserved for high-end applications like armour systems in helicopters and submarines.
b. Pressureless Sintering:
- Lower Density: Pressureless sintering typically achieves only 80%-87% relative density, even at temperatures between 2250-2300°C.
- Cost-Effectiveness: This method is more economical but is generally less effective for high-performance applications.
4. The Role of Density in Bulletproof Ceramics:
The density of the ceramic material plays a crucial role in its effectiveness as bulletproof armour. Higher density usually translates to higher hardness and, consequently, better performance against ballistic threats.
a. Importance of High Density:
- Increased Hardness: Higher density leads to increased hardness, which is vital for shattering incoming projectiles.
- Fine-Grained Structure: A high-density, fine-grained structure enhances the material’s overall strength, making it more effective against various forms of impact.
5. Comparative Analysis: Hot-Pressing vs. Pressureless Sintering:
Understanding the nuances between hot-pressing and pressureless sintering is crucial for selecting the right method for your specific application. This section provides a comparative analysis of both.
a. Mechanical Properties:
- Compressive Strength: Hot-pressing generally results in higher compressive strength due to the higher density achieved.
- Flexural Strength: Pressureless sintering may offer better flexural strength, making it more suitable for applications that require flexibility.
b. Thermal Properties:
- Thermal Conductivity: Hot-pressed boron carbide exhibits higher thermal conductivity, beneficial for high-temperature applications.
- Thermal Expansion: Pressureless sintered boron carbide has a lower coefficient of thermal expansion, making it more stable under varying temperature conditions.
c. Economic Considerations:
- Production Costs: Hot-pressing is more expensive due to the specialized equipment and higher energy consumption.
- Scalability: Pressureless sintering is more scalable and cost-effective for large-scale production.
6. Case Studies:
Real-world applications of boron carbide in bulletproof ceramics have demonstrated the effectiveness of both hot-pressing and pressureless sintering methods. These case studies provide valuable insights into the practical implications of each method.
a. Military Applications:
- Hot-Pressed Armor: Used in specialized military vehicles and aircraft for maximum protection.
- Pressureless Sintered Armor: Commonly used in body armor due to its lighter weight and cost-effectiveness.
b. Industrial Applications:
- Hot-Pressed Components: Utilized in industrial cutting tools and abrasives.
- Pressureless Sintered Components: Used in wear-resistant applications like seals and bearings.
7. Conclusion:
Choosing between hot-pressing and pressureless sintering for boron carbide bulletproof ceramics involves a careful consideration of mechanical and thermal properties, as well as economic factors. By understanding the advantages and limitations of each method, you can make an informed decision tailored to your specific needs.
8. Contact Details:
For further inquiries and tailored solutions in bulletproof ceramics, please reach out to us.
Email: rongqi.chen@moatcity.com
Web: www.moatcity.com
WhatsApp: +447983626714
We look forward to assisting you with your bulletproof ceramics needs.
Leave a Reply